Training in ISO 17025:2017 and laboratory disciplines Maintech Calibrators Pvt. Ltd. involves gaining a deep understanding of both the management system (ISO 17025) and the technical aspects related to measurement and calibration of various parameters like force, mass, and temperature. Here’s an overview of what such training typically entails:
Introduction to ISO 17025:
ISO 17025:2017 is the international standard that specifies the general requirements for the competence of testing and calibration laboratories. It is applicable to laboratories that perform tests and calibrations in any field of science and technology.
Key Sections of ISO 17025:
Management Requirements:
Organization and responsibility (including the role of quality managers).
Document control and records management.
Internal audits, corrective actions, and continuous improvement.
Proficiency testing and external audits.
Technical Requirements:
Personnel: Competence requirements for laboratory personnel (qualifications, training, and skills).
Accommodation and Environmental Conditions: Laboratory environment and equipment must be suitable for testing and calibration.
Test and Calibration Methods: Procedures for validating and verifying test and calibration methods, and ensuring their accuracy and reliability.
Equipment: Requirements for equipment maintenance, calibration, and traceability.
Measurement Traceability: Ensuring that measurements can be traced to national or international standards.
Reporting Results: How to report the results and uncertainties, as well as handling nonconformities.
Practical Implementation of ISO 17025:
The training includes practical exercises where participants learn how to implement the requirements of ISO 17025 in a laboratory setting. This may include conducting internal audits, reviewing SOPs, and practicing calibration techniques.
This part of the training focuses on the technical competence needed for accurate measurements and calibration in the specific fields of mechanical metrology, force metrology, mass metrology, and thermal metrology.
Mechanical Metrology
Measurement of Physical Dimensions:
Training on tools like micrometers, calipers, and coordinate measuring machines for measuring dimensions such as length, width, height, and diameter.
Gear and Thread Measurements:
Tools like gear analyzers and thread gauges for measuring mechanical components.
Error Measurement and Calibration:
Training in identifying and correcting measurement errors in mechanical systems and understanding uncertainty in measurements.
Force Metrology
Force Measurement Techniques:
Use of force transducers, load cells, and other equipment to measure forces accurately. Understanding calibration techniques for these devices.
Force Calibration:
The procedures for calibrating force measurement devices, ensuring traceability to national or international standards (e.g., using a dead weight tester).
Uncertainty in Force Measurements:
Understanding and calculating the uncertainty of force measurements and applying correction factors.
Mass Metrology
Mass Calibration:
Calibration of mass standards (weights) using precision balances and the use of certified reference materials (CRMs).
Traceability:
Ensuring the traceability of mass measurements to national standards, such as the International System of Units (SI).
Weighing Techniques:
Proper techniques for using high-precision balances, including calibration, verification, and error management.
Uncertainty Analysis:
Analyzing uncertainty in mass measurements, including environmental factors like humidity and temperature.
Thermal Metrology
Temperature Measurement:
Understanding and using various types of thermometers (e.g., resistance thermometers, thermocouples, infrared thermometers) for precise temperature measurements.
Calibration of Temperature Sensors:
Methods for calibrating temperature sensors using fixed-point calibration or comparison to a known standard.
Thermal Calibration Equipment:
Use of specialized equipment such as temperature baths, black-body radiators, and furnaces for the calibration of thermometers.
Uncertainty in Temperature Measurements:
Calculating the uncertainty in temperature measurements, including factors like sensor accuracy, environmental conditions, and calibration equipment reliability.
Documenting Procedures and Results:
Ensure that all the calibration and testing activities are documented according to ISO 17025 guidelines, including test methods, measurement uncertainty, and results.
Traceability:
Ensuring all measurements and calibrations are traceable to national or international standards, with proper records maintained for quality assurance.
Proficiency Testing and Inter-laboratory Comparisons:
Participation in proficiency testing programs to ensure the accuracy of measurements and compliance with ISO 17025.
Internal Audits and Continuous Improvement:
The laboratory’s quality management system (QMS) should include regular internal audits and actions for corrective measures to meet the standard’s requirements.
Conclusion:
ISO 17025:2017 training for a mechanical, force, mass, and thermal laboratory encompasses both theoretical and practical aspects. The focus is on ensuring that laboratories meet international standards for competence, quality, and traceability in testing and calibration processes. This ensures that measurements in these critical fields are accurate, reliable, and consistent with global standards.
The training may be conducted through workshops, seminars, hands-on practice sessions, and audits, and it is aimed at laboratory personnel, quality managers, and others involved in the management or technical aspects of laboratory operations.
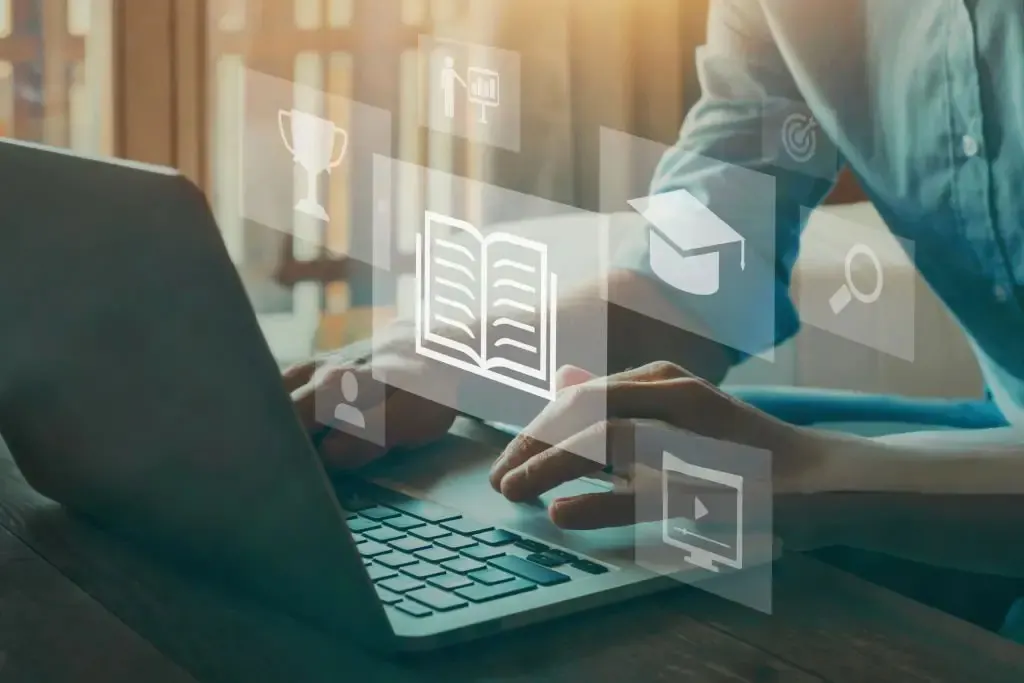